Company News
Sep 2, 2019
SERFOW PROJECT
SERFOW stands for Smart Enabling Robotic Driving Free Form Welding. This project aids the development of a highly configurable free-form welding system for the repair and manufacture of high-value aerospace and nuclear industry components.
This project features our Smart Grasping System which includes our 3 fingered Modular Grasper. The development of the Modular Grasper was supported by the European Commission under contracts H2020-FoF-2016.723853 (COROMA) and H2020-PHC-2014-single-stage (RAMCIP)
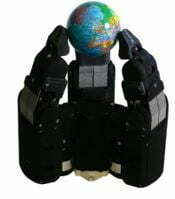
Project Title:
SERFOW
Project Duration:
2017-2018
Project Facilitators:
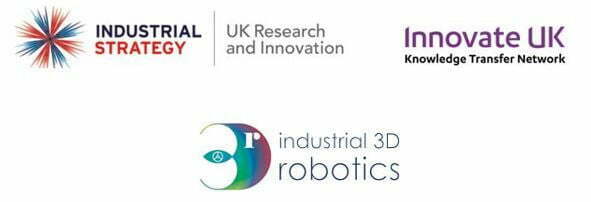
Project Collaborators:
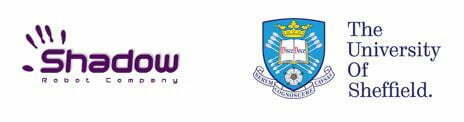
Project Overview:
This project involves the development of a highly configurable free-form welding system for the repair and manufacture of high-value aerospace and nuclear industry components that require typical TIG welding techniques as well as additive manufacturing techniques. Additive Manufacturing (AM) is predicted to be a significant growth area with the potential to completely redefine manufacturing in key sectors (nuclear, aerospace and automotive). New procedural models are required to implement effectively, producing significant benefits such as the reduction of material waste, fewer production steps and fewer distinct parts required for an assembly.
For new AM techniques, such as energy directed deposition to become widely adopted across all manufacturing sectors, new autonomous, dynamic and flexible multi-tooled robotic platforms are required to perform complex tasks such as welding. These platforms need to be responsive to a plethora of real-time process variables, and have the capability to work within a variety of operational environments with minimum human intervention.
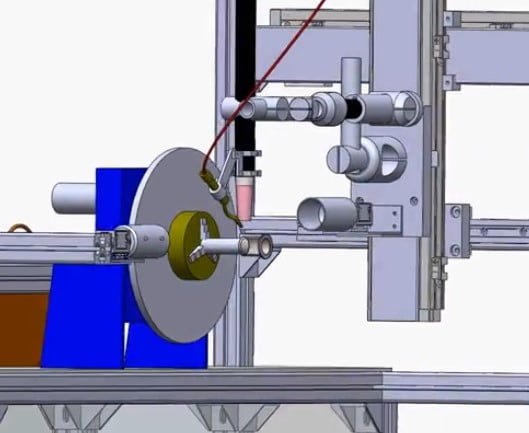
Project Details:
Current manufacturing methods are inflexible, often requiring the time-intensive pre-programming of production tasks. This methodology works well until a part-update or a short run of a new part is required, in which case the replacement of expensive welding jigs and time-consuming setup by expert staff is required.
The aim of the SERFOW project was to produce a flexible and dynamic free-form welding system that can provide low-cost additive manufacturing support. The platform can identify individual parts using an advanced stereo camera system, which is partnered with a robotic arm and TIG welding set to produce an intelligent and flexible manufacturing platform. The repair and manufacture of high-value aerospace and nuclear industry components on short time scales, and at low-cost, can be achievable.
We worked on the development of a system which has the flexibility to produce structures using weld filler deposition, and to produce mechanical joints between discrete parts. The SERFOW system can be integrated with different types of welding technology and will be capable of working on parts of all shape and sizes autonomously – a feat which is beyond that of existing commercially available systems.
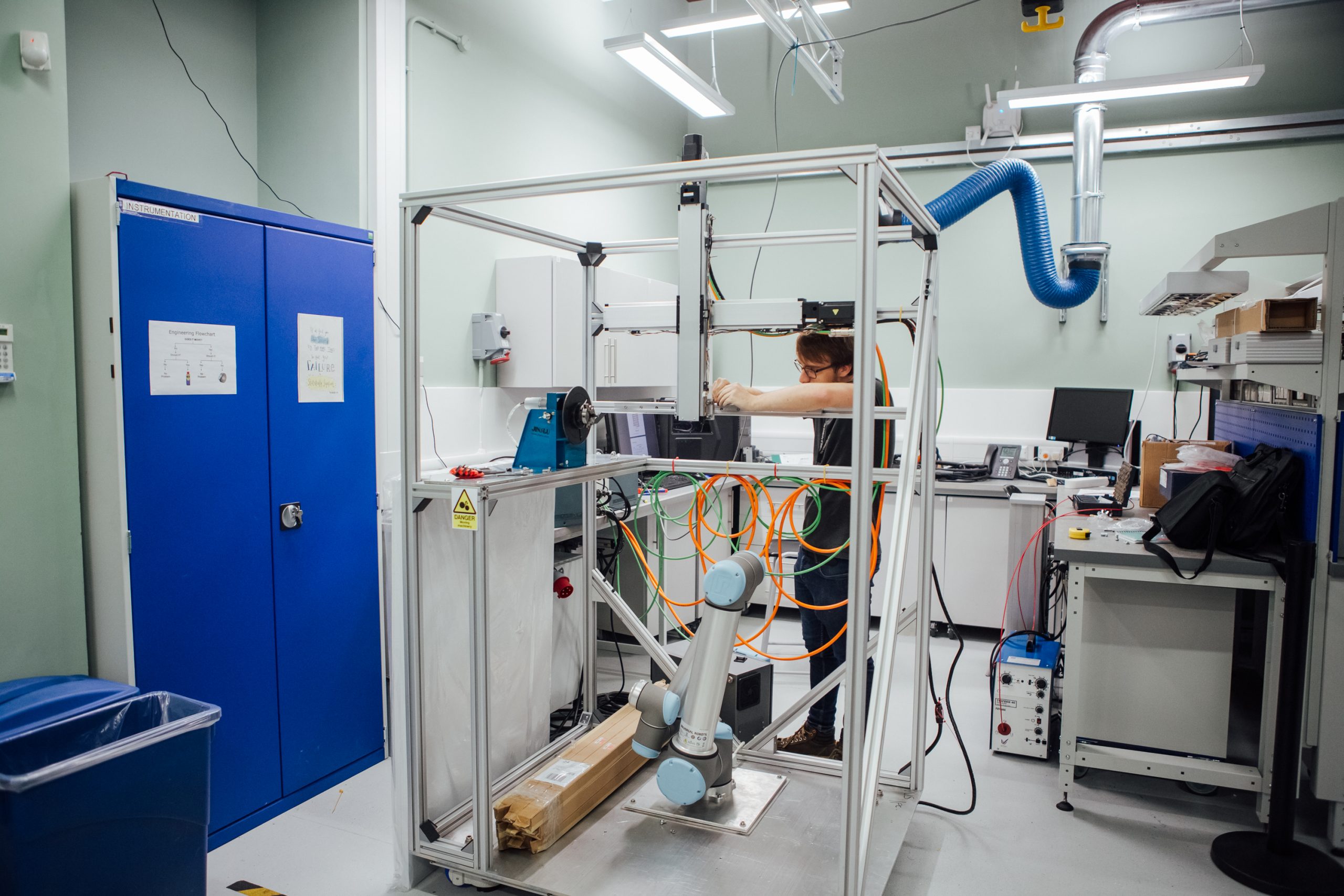
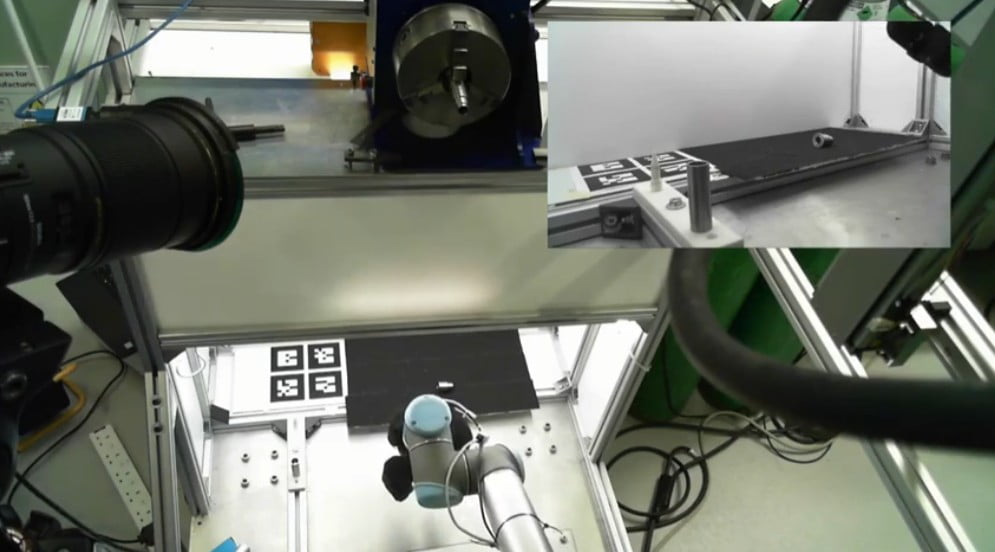
Project Conclusions:
This flexible manufacturing approach to autonomous AM design allows the rapid and dynamic alteration of a production task, which is of critical importance to the aerospace, nuclear and petrochemical industries. Parts that consist of unique shapes, profiles and sizes can be readily altered without the usual tooling and redesign costs. Not only will the automated process result in direct cost savings for industry, it will also allow for greater process refinement during welding.
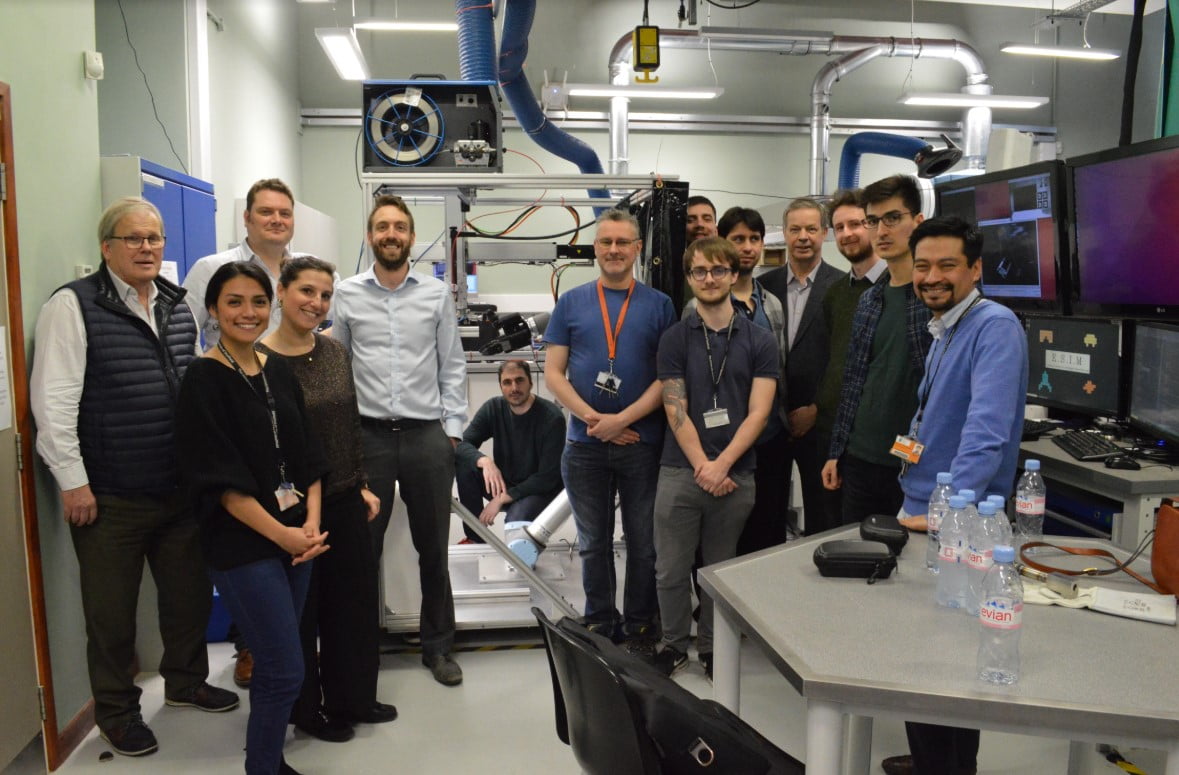
If you have any questions regarding the project or any of our products, feel free to get in touch by emailing contact@shadowrobot.com or calling us on +44 (0)20 7700 2487